High-Pressure Flanges: Everything you need to know
High-pressure flanges are essential components in industries where the equipment must withstand extreme conditions, including high pressures and temperatures. At Marcel Piping Projects Supply PVT. LTD., we specialize in providing high-quality high-pressure flanges that meet the rigorous demands of various sectors, including oil & gas, petrochemicals, power generation, and more.
In this blog, weโll explore the specifications, grades, standards, and types of high-pressure flanges, offering valuable insights for purchasers looking to make informed decisions.
What Are High-Pressure Flanges?
High-pressure flanges are designed to connect pipes, valves, pumps, and other equipment under extreme conditions. These flanges are built to withstand high pressures and temperatures, ensuring the safe and efficient operation of industrial systems.
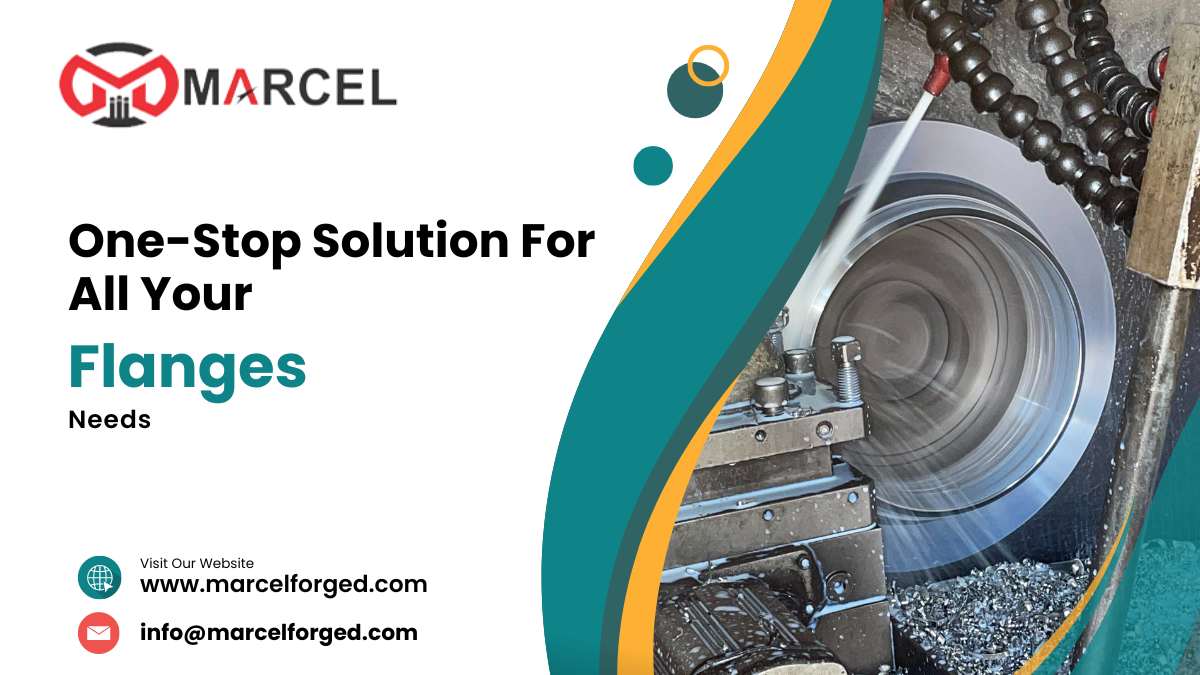
High-Pressure Flanges – Everything you need to know
Key Specifications of High-Pressure Flanges
- Pressure Rating:
- High-pressure flanges are typically rated for classes such as 600, 900, 1500, 2500, and even higher, depending on the application.
- The pressure rating is determined based on the flange’s material, design, and application conditions.
- Temperature Rating:
- High-pressure flanges can handle a wide range of temperatures, from cryogenic conditions to elevated temperatures, depending on the material used.
- Materials like stainless steel and alloy steel are preferred for high-temperature applications due to their excellent thermal stability.
- Material:
- Common materials used include carbon steel, alloy steel, stainless steel, and duplex/super duplex steel.
- The choice of material is critical as it affects the flange’s ability to resist corrosion, oxidation, and mechanical stress.
- Dimensions:
- Dimensions of high-pressure flanges are standardized by organizations like ASME, ensuring compatibility and interchangeability in global applications.
- Typical dimensions include the outer diameter (OD), thickness, bolt circle diameter, and bolt hole size.
Material Grades for High-Pressure Flanges
- Carbon Steel Grades:
- ASTM A105: Commonly used for forged carbon steel piping components.
- ASTM A350 LF2: Suitable for low-temperature service.
- Stainless Steel Grades:
- Alloy Steel Grades:
- ASTM A182 F5, F9, F11, F22, F91: These are chromium-molybdenum alloy steels known for their high strength, toughness, and resistance to high temperature.
- Duplex and Super Duplex Steel Grades:
- UNS S31803, UNS S32205: Provide high resistance to pitting and crevice corrosion, making them ideal for aggressive environments.
- Inconel and Other High-Alloy Materials:
- Inconel 625, Inconel 718: Used in applications where both high strength and corrosion resistance are required.
Standards Governing High-Pressure Flanges
- ASME B16.5:
- This standard covers pipe flanges and flanged fittings for sizes NPS 1/2 through NPS 24.
- It specifies pressure-temperature ratings, materials, dimensions, tolerances, marking, and testing.
- ASME B16.47:
- Covers large diameter steel flanges for sizes NPS 26 through NPS 60.
- This standard is divided into two categories: Series A (MSS SP-44) and Series B (API 605).
- API 6A:
- Specifically designed for flanges used in wellhead and Christmas tree equipment.
- Focuses on equipment used in high-pressure oil and gas drilling and production.
- DIN and EN Standards:
- European standards like DIN 2501, EN 1092-1, also cover specifications for high-pressure flanges.
- These standards are often used in international projects requiring compliance with European regulations.
Types of High-Pressure Flanges
- Weld Neck Flanges (WN):
- Designed to withstand high pressures and temperatures, weld neck flanges are welded to the pipe, providing excellent stress distribution.
- Commonly used in pipelines, pressure vessels, and high-pressure systems.
- Blind Flanges:
- Used to seal off the ends of pipes, valves, or pressure vessel openings.
- Blind flanges are ideal for high-pressure applications where a secure, leak-proof seal is required.
- Socket Weld Flanges:
- Designed for smaller pipe sizes, socket weld flanges are used in high-pressure systems where strong, durable connections are needed.
- The pipe is inserted into the flange’s socket and then fillet welded.
- Slip-On Flanges:
- These flanges are slipped over the pipe and then welded both inside and outside to provide strength.
- While generally not as strong as weld neck flanges, slip-on flanges are easier to install and align.
- Lap Joint Flanges:
- Used with stub ends, lap joint flanges are not welded directly to the pipe, making them ideal for systems where frequent disassembly is required.
- They offer flexibility in high-pressure systems where the flange must be adjusted or removed.
- Orifice Flanges:
- Used in conjunction with orifice plates to measure the flow of liquids or gases in high-pressure pipelines.
- Orifice flanges come with a tapped hole for pressure measurements and are crucial in metering systems.
- RTJ (Ring Type Joint) Flanges:
- Designed for high-pressure, high-temperature applications, RTJ flanges provide a metal-to-metal seal using a gasket.
- Commonly used in the oil and gas industry, RTJ flanges ensure a leak-proof connection under extreme conditions.
Applications of High-Pressure Flanges
- Oil & Gas Industry: Used in upstream, midstream, and downstream applications, including drilling rigs, pipelines, and refineries.
- Power Generation: High-pressure flanges are critical in steam turbines, boilers, and heat exchangers.
- Petrochemicals: Used in reactors, pressure vessels, and piping systems where harsh chemicals and high pressures are common.
- Chemical Processing: High-pressure flanges are employed in chemical plants where strong acids, alkalis, and high temperatures are present.
- Aerospace: Used in high-pressure hydraulic and fuel systems, where reliability and safety are paramount.
Choosing the Right High-Pressure Flange
When selecting a high-pressure flange, consider the following factors:- Material Compatibility: Ensure the material is suitable for the fluid or gas being transported and the environmental conditions.
- Pressure Rating: Choose a flange with an appropriate pressure rating for your systemโs operating conditions.
- Temperature Rating: Verify that the flange can withstand the maximum temperature in your application.
- Corrosion Resistance: For corrosive environments, select materials with high resistance to corrosion.
- Compliance with Standards: Ensure the flange complies with the relevant industry standards for safety and reliability.